Temple and Eleri LLC exploring impact resistant lithium-ion battery cell
Nathan Snizaski
Oct 6, 2022
The transportation industry is increasingly turning to lithium-ion batteries, but as their use rises, safety concerns do as well. Lithium-ion battery failure can be catastrophic, whether in the airline, electric vehicle, or cellphone industry. Today's commercial lithium-ion battery cells consist of two electrodes and a separator. The electrodes are comprised of a thin metal foil substrate, or current collector, coated with active and anode and cathode particles. A microporous polymeric film, called the separator, separates the two electrodes to prevent an internal short circuit.
However, this separator can't always handle mechanical strain, which leads to short circuit and failure, which is why this collaboration between Temple University and Eleri LLC focused on a model-based design and prototype for an advanced lithium-ion battery with a significant improvement under mechanically abusive loading condition. Instead of traditional metal foils, the team sought to develop a core technology: an impact resistant, three-dimensional metal substrate.
"In any type of car, safety is a critical concern," says Eric Carlson, chief executive office and co-founder of Eleri, LLC. "We have safety belts and air bags, and when we look at protecting passengers, we apply those same safety concerns to the battery.” Car companies are introducing electric vehicles and build electric structures around the battery pack to protect it in the event of the crash. “The protection is key, because if an internal short occurs during a crash, and the battery isn't properly protected, it can catch on fire."
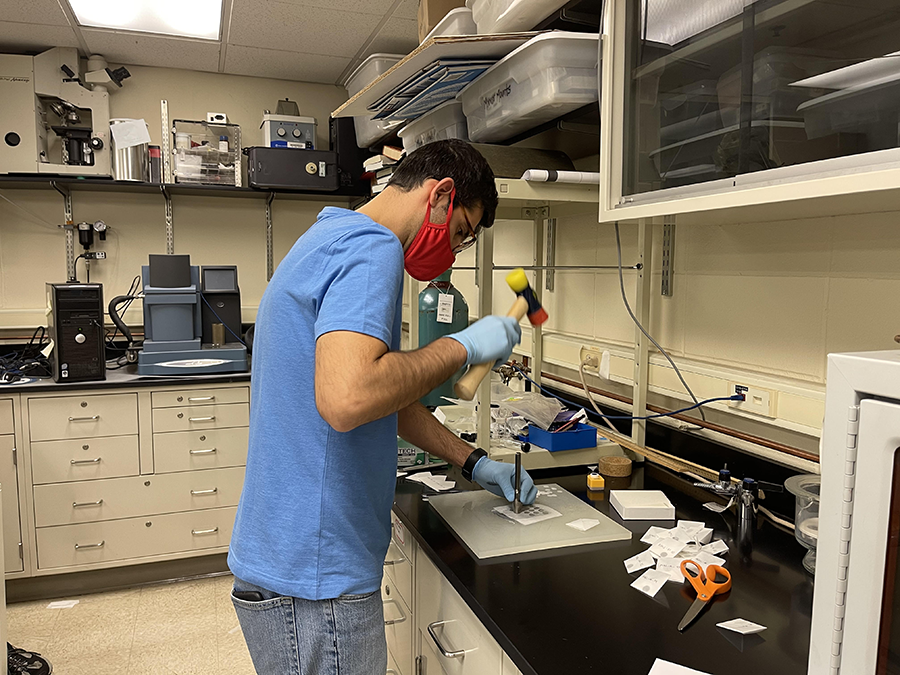
Source: Temple University
Manufacturing PA participant Mohammad Keshavarzi (Ph.D. Student)
"The technology that we're looking at will make the battery inherently more robust to mechanical deformation," Carlson explains. "The benefit for car companies is that the battery packs and vehicle structures will be reduced in terms of both weight and volume, which reduces cost, as well as the weight of the vehicle, which is directly related to the range of the vehicle and the charging required. Naturally, if you can reduce cost and increase safety, ideally that will help to facilitate the adoption of a technology."
"It has been wonderful working with Eric through Eleri LLC,” says Elham Sahraei, associate professor of mechanical engineering at Temple University and fellow co-founder of Eleri LLC. "Not only does he have extensive knowledge of the electrochemical processes in the battery, but he has also brought very good advisors to our team. Along with his own knowledge, he brings knowledge of others as well. I think anyone working with him is very lucky."
I had the chance to work with some of the brightest minds in the lithium-ion batteries field who helped to shape me into a multi-disciplinary engineer/researcher.
Mohammad Keshavarzi, Ph.D. student, Temple University
Part of Sahraei’s lab, Temple University Ph.D. student Mohammad Keshavarzi credits the Manufacturing PA program for gaining valuable industry experience through the collaboration. Specifically, the project granted Keshavarzi the opportunity to supplement his knowledge of battery modeling with a deeper understanding of the electrochemical processes happening inside of the batteries and the hands-on experience in the manufacturing of anode and cathode layers. “These skill sets helped to shape my understanding of the lithium-ion battery manufacturing process and paved the way for me to incorporate my mechanical background toward the development of more mechanically robust lithium-ion batteries,” says Mohammad. “Along the way, I had the chance to work with some of the brightest minds in the lithium-ion batteries field who helped to shape me into a multi-disciplinary engineer/researcher.”